Modern Technology Behind RMI Sugar Production
Rejoso Manis Indo, 08 September 2022 | Penulis : Muhamad Devi Riswandi
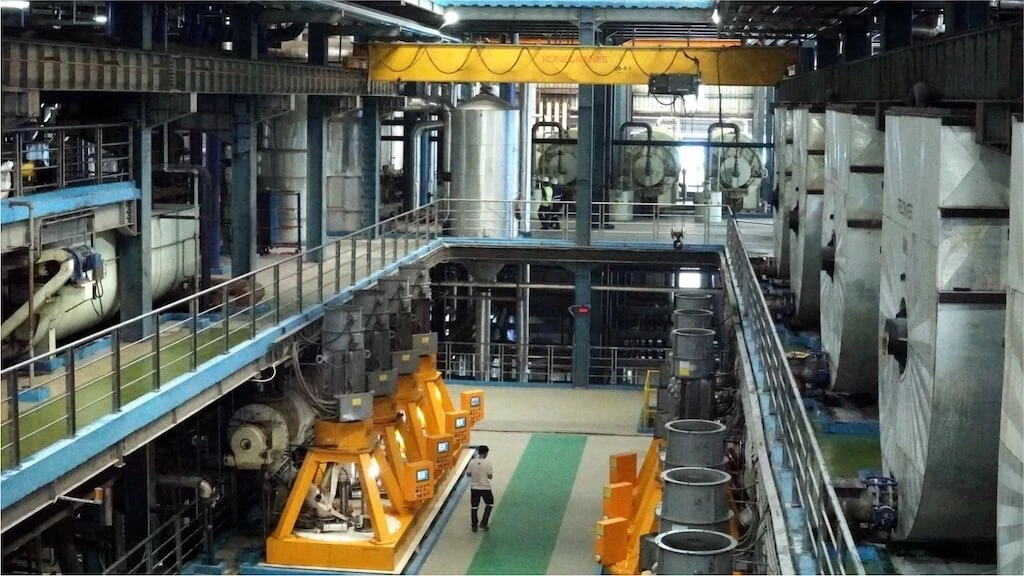
Sugar Factory (PG) PT Rejoso Manis Indo (RMI) produces high quality sugar. The sugar product produced by the factory located in Rejoso Village, Binangun District, Blitar Regency, has passed a number of quality certifications.
Sugar Factory (PG) PT Rejoso Manis Indo (RMI) produces high quality sugar. The sugar product produced by the factory located in Rejoso Village, Binangun District, Blitar Regency, has passed a number of quality certifications.
Domestically, PG RMI has received a certificate of Indonesian National Standard (SNI), a certificate from the Food and Drug Supervisory Agency (BPOM) and a Halal Assurance System certificate of 23000 from the Institute for the Study of Food, Drugs and Cosmetics (LPPOM) of the Indonesian Ulema Council (MUI).
Certificates also come from the International Organization for Standardization (ISO). To PG RMI, the global organization gave the certificate of Quality Management Standard ISO 9001:2015.
This achievement cannot be separated from the latest machinery technology at PG RMI which is manned by trained human resources and effective management. What are the machines in PT RMI's factory?
1. Tandem Mill Set (Milling)
The tandem mill set at PG RMI is a complete set of sugarcane milling equipment ordered from Bundaberg Walkers, Australia. RMI chose it based on several considerations.
First, because it is the most popular in the world. Second, because the maintenance can be done at PG RMI or remotely from the factory in Australia. Third, because its reliability has been tested. Fourth, because the control system integrates the operation of all equipment with high efficiency.
The following is a brief description of a series of production processes carried out in a tandem mill set:
At first several sugarcane trucks occupied the unloading position. Then the tipper machine flips the truck backwards almost 90 degrees so that the load falls onto the conveyor (side cane carrier).
The sugar cane then moves to the mill house. There are many stages that sugar cane must pass there.
Initially, the sugar cane was leveled using a leveller machine, then it was transferred to the main cane carrier.
In the main cane carrier, sugar cane is chopped (chopped) in two stages, namely in the cutting knife unit (cutter) 1 and cutter 2. The result is a short cane stalk which is then transported by a belt conveyor to the shredders for grinding.
From the shredders, the sugar cane is carried through an elevator to the mill machine for squeezing. Squeezing is carried out in 5 stages in 5 mill sets. The result is sap (sugar cane syrup) and bagasse (dregs). The sap will be further processed into sugar, while the bagasse is used as fuel for the boiler.
2. Process Station
The Process Station is in charge of further processing the milky juice received from the milling station (tandem mill set). The task was carried out with modern equipment imported from Sutech, Thailand.
The following is a brief overview of how these devices operate:
First, the sap is sent to the purification unit to be separated from the impurities (blothong). The result is a clear sap.
Second, the clear juice is then evaporated in the evaporation unit. The result is concentrated sap (raw syrup) which looks dark.
Third, the dark and concentrated juice is then sent to boiler 1 to be cooked (using steam) to increase its concentration again so that crystals appear.
Fourth, the solution which already contains these crystals then enters the centrifugal unit 1 to be melted.
Fifth, the smelting product goes into the purification unit again (remelt) using carbonation (a kind of vessel that is fed with CO2 from the boiler).
Sixth, the remelted carbonate is sent to boiler 2 to be cooked again. There is a refinery going on here. The result is a whiter crystal.
Seventh, the refined crystals are sent to centrifugal unit 2. Here the crystals are separated from the liquid.
Eighth, the crystals processed in centrifuge 2 are then dried and cooled. After that it is sent to the packaging (bagging) station.
3. Robotic Bagging
Before being brought to the storage warehouse, the white crystal sugar grains are packed at the Packaging Station. Initially, the items sent from the Process Station were accommodated in the product bin, then packaged in plastic sacks, each with a capacity of 50 kg.
The sack is equipped with an inner bag. The goal is to keep the sugar clean and the sugar moisture so it doesn't melt and break easily.
Packaging is done robotically (robotic bagging). This process begins with sack picking, sack filling, digital weighing, sack sewing,
to delivery to the transport vehicle.
In this process there is a metal detector to ensure the product does not contain metal elements. If metallic elements are found, the product will automatically shift to another line for further inspection.
The robotic bagging technology imported by PG RMI from Statec Binder, Austria, is operated and controlled by trained human resources (HR) who use Occupational Health and Safety (K3) equipment.
4. Boiler and Turbine Generator
Large sugar mills like RMI need a lot of energy to operate. And the energy supply at the RMI plant is supplied independently by the power house. Both the need for heat energy sources for sugar processing and energy sources for power generation.
How does it work? The key is in the boiler (made in Thermax, India) and turbine generator (made in Triveni, India).
In the boiler, water is heated with bagasse fuel. The result of the heating is in the form of high pressure steam which then flows into the powerhouse unit to drive the turbine. The turbine then drives the generator.
It is from this generator that electricity is generated. Its large power, which is 2x12 megawatts, is sufficient to meet all electricity needs in the factory.
Besides being used as a power plant, the steam produced by the boiler is also used at the processing station as a source of heat energy for sugar cooking, carbonation, and crystallization.
5. Laboratory Quality Control
Everything related to production at PG RMI is tested and analyzed here, from raw materials (sugarcane), materials for the production process, water quality, to sugar and molasses (cane molasses).
Tests are carried out chemically and physically, then analyzed using tools that are supported by digital methods so that the accuracy is very high. For example, the sugar content (polarization), which in the RMI is determined to reach 99 percent, can be analyzed in this laboratory precisely.
Likewise the yield, boiler feed water, and drops; all analyzed using digital equipment to ensure compliance with specified parameters.*
Most Popular
1
How Cane Is Processed into Sugar at PT RMI's Factory
2
The Interest of Blitar Sugarcane Farmers Continues to Increase, Here's Why
3
PT RMI and the Story of the Return of the Sugar Factory in Blitar
4
Modern Technology Behind RMI Sugar Production
5
Profitable Programs for Partner Farmers
6
Buy-and-Set System Profits Sugar Cane Farmers
7
Vacancies for you professionals in the Purchasing field
8
High Efficiency of Sugar Production in Rejoso, Blitar
9
Sugar in the Global Market
10
Blitar Regency Government and PT RMI - Mitr Phol Group Collaborate with ITS Civil Engineering Faculty Expert Team to Conduct Feasibility Test Study for Road and Bridge Classes
11
PT RMI's Environmentally Friendly Operations
12
The Ministry of Industry Appreciates PT RMI - Mitr Phol Group in Efforts to Develop the National Sugar Industry