High Efficiency of Sugar Production in Rejoso, Blitar
Rejoso Manis Indo, 03 October 2022 | Penulis : Muhamad Devi Riswandi
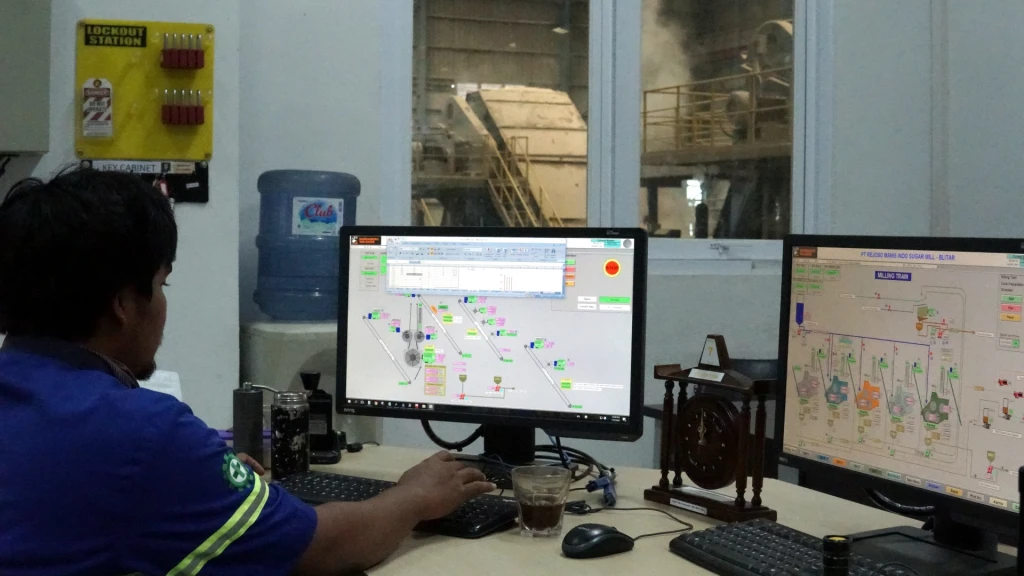
PT RMI's PG production management is carried out digitally, computerized, and integrated so that modern equipment with advanced technology can operate optimally effectively and efficiently. An activity can be seen in one of the control rooms at PG RMI.
Sugar Factory (PG) PT Rejoso Manis Indo (RMI) produces sugar with high efficiency. One of the keys to efficiency lies in production management which is supported by modern equipment with advanced technology. Equipment and machinery from world-class leading manufacturers are assembled integrated in such a way that overall increases performance, productivity and reduces costs.
At the mill station, for example, the extraction of sugarcane juice or sugar cane syrup can be maximized to the extent that it leaves dry bagasse (bagasse) with no more than 1 percent remaining sugar content of its volume. This can happen because the extraction of sugarcane juice is carried out in several stages.
Then efficiency at the bagging station. Here, with robotic bagging technology, PG RMI can prepare ready-to-sell products at high speed. As much as 1,500 tons of product can be packed in a day.
Powerful Powerhouse
Availability of heat energy and large electrical energy is absolutely needed in producing sugar. Heat energy for sugar cooking, carbonation, and crystallization. Meanwhile, electrical energy is used to operate all existing equipment.
These needs are supplied by powerhouses that use state-of-the-art boilers, turbines and generators. Thanks to these equipment, PG RMI is able to produce its own energy needed for all its production activities, both thermal energy and electrical energy.
The energy base is bagasse (bagasse), so PG RMI does not have to depend on coal as an energy source. Coal is only imported and used as a reserve, when the supply of sugar cane is not sufficient.
Digitization, Computerization, Integration
Sugar production management at PG RMI utilizes advances in digital technology and integrated computer networks. This technology makes important decisions related to sugar production easy and fast. This makes production management performance more effective and efficient.
An example can be seen in the tandem mill set. Here there is a special room called the Distributed Control System (DCS) room. DCS is a control system in charge of retrieving and processing data, and based on that data performs integrated control over the operation of all equipment at the milling station, including control of the speed of sugarcane rate from one processing station to the next.
These high-precision integrated controls are neatly computerized. All operation buttons are available on the monitor screen display so that the operator simply clicks the button as needed. For example, click the Start button to start the milling operation and the Stop button to stop it.
With digital systems and computer networks, PG RMI has also succeeded in streamlining and streamlining the performance of each production unit. They can exchange data without having to physically move from one unit to another.
This facility is closely related to the quality control laboratory. This laboratory is in charge of analyzing or testing all matters related to production (sugar cane raw materials, process auxiliary materials, water quality, sugar, molasses, and others). The analysis was carried out using digital equipment according to the specified parameters with a high degree of accuracy.
All results of the analysis are reported through an internal website network that can be accessed by related parties (milling stations, process stations, packaging stations, and others).
Data updates from the laboratory are carried out every 1 hour, every 2 hours, or every 4 hours; according to the needs. Materials analyzed per 1 hour include raw syrup, first juice, mixed juice, clarified juice, and bagasse. Materials analyzed every 2 hours, for example, raffinated sugar, final molasses, and condensate. While those analyzed every 4 hours, among others, raw sugar and final molasses.
Sharing information on the results of this periodic analysis is very useful for related parties. They can get a real and actual picture related to their task of carrying out the right and fast treatment, simply by accessing the website.*
Most Popular
1
How Cane Is Processed into Sugar at PT RMI's Factory
2
The Interest of Blitar Sugarcane Farmers Continues to Increase, Here's Why
3
PT RMI and the Story of the Return of the Sugar Factory in Blitar
4
Modern Technology Behind RMI Sugar Production
5
Profitable Programs for Partner Farmers
6
Buy-and-Set System Profits Sugar Cane Farmers
7
Vacancies for you professionals in the Purchasing field
8
High Efficiency of Sugar Production in Rejoso, Blitar
9
Sugar in the Global Market
10
Blitar Regency Government and PT RMI - Mitr Phol Group Collaborate with ITS Civil Engineering Faculty Expert Team to Conduct Feasibility Test Study for Road and Bridge Classes
11
PT RMI's Environmentally Friendly Operations
12
The Ministry of Industry Appreciates PT RMI - Mitr Phol Group in Efforts to Develop the National Sugar Industry